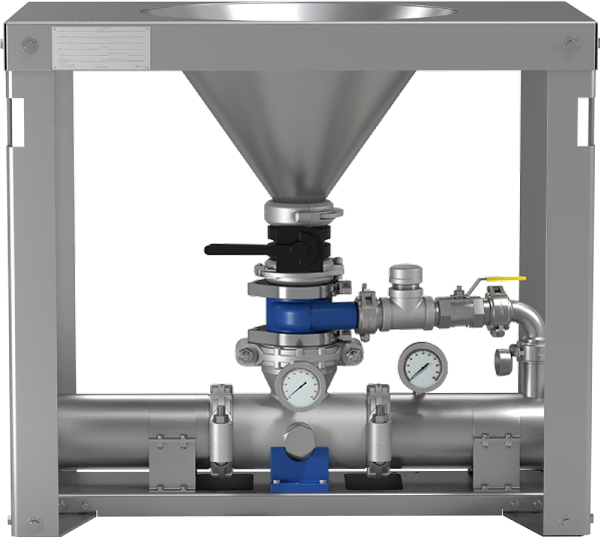
Lobestar® Shear-Mixer
The Lobestar® Shear-Mixer is a high-performance Venturi eductor designed for demanding slurry mixing applications, including
• oil & gas drilling fluids
• construction material production
• chemical production mining
• sugar solution mixing
• brine mixing
• cosmetics
• paint pigment mixing
• metal processing
• plastic production
• and more.
It provides higher additive loading rates and more complete mixing than traditional Venturi eductors, and contains no motorized or rotating components. This streamlined design makes the Lobestar® Shear-Mixer extremely resistant to plugging, reducing downtime. Dual suction port options provide added versatility for simple installation and seamless integration into existing mixing systems.
Highly Customizable
Versatile Applications
Prevents Clumps
Direct, Simple Installation
No moving parts
Direct, Simple Installation
Superior additive loading rates
Reduced Clogging
Handles hard-to-mix clays and polymers
Mix Reliability With Versatility
From mud mixing and drilling fluids to pharmaceuticals and cosmetics, the Lobestar® Shear-Mixer meets the rigorous demands of industrial applications. Watch the Shear-Mixer in action to discover its superior mixing performance.
Products
Discover More Vortex Products
Explore a range of best-in-class Vortex Ventures products that turn your solvents into solutions.
-
MixMate
Harsh chemical mixing barrel for safe, rapid, homogenous mixing in tough industrial applications.
-
Radial Eductor
Tank mixing eductors for various mixing purposes, with simple, compact designs and no required maintenance.
-
Dust Recovery System (DRS)
Safety-enhancing system with passive product recovery to reduce dust emission into nearby environments.
Frequently Asked Questions
Browse answers to common questions about Lobestar Shear-Mixer and processes.
Why is the Lobestar® Shear-Mixer much more resistant to plugging than regularventuri eductors?
The unique design of the Lobestar® Mixing Nozzle creates an open path for solid additives to enter the mixing chamber with no obstructive, protruding nozzle on which to accumulate and bridge.
What concentration of solids to liquid can be achieved with the Lobestar® Shear-Mixer?
Typically, 1-3 pounds of solids per each gallon of motive liquid is achievable. The bulk density, solubility, absorbency, and flow characteristics of the specific solid additive all factor into the actual, achievable concentration ratio. Motive liquid properties such as saturation or solubility also have an impact on the achievable concentration ratio.
What factors determine if a Lobestar® Shear-Mixer can work for my application?
A) Motive liquid viscosity of 300 centipoise (1475 SSU) or less. Higher viscosity levels have a negative impact on Lobestar® Shear-Mixer function.
B) Existing discharge piping diameter and geometry. The discharge piping diameter should be at least as large as the diameter of the Lobestar® Shear-Mixer from the mixer to the discharge point. The pressure loss throughout the discharge piping should be minimized by keeping the overall length as short as possible, maintaining a low vertical lift, keeping the number of elbows and fittings to a minimum, and/or increasing the pipe size if possible.
C) Motive head differential across the mixer. Optimum function of the Lobestar® Shear-Mixer requires a motive head differential between 115 – 185 feet of motive head.
How should additives be fed into the Lobestar® Shear-Mixer?
Ideally, additives should be fed into the open Lobestar® Shear-Mixer suction port steadily and gradually. Flooding the hopper or funnel connected the suction port with additives is not optimal since this has potential to cause overflow if the hopper is not designed to avoid bridging or ratholing.
How is the Radial Premixer different than a typical washdown nozzle used with regular venturi eductors?
The Radial Premixer is integrated with the Lobestar® Shear-Mixer suction port and is designed to create a fluid vortex that not only washes down additives and forms a liquid barrier to the atmosphere, but also prevents fisheyes from forming in the mixed slurry.
When is a Radial Premixer on the Lobestar® Shear-Mixer required?
The Radial Premixer is required whenever using the Lobestar® Shear-Mixer to mix sticky, hydrophilic additives that swell, cake or form fisheyes when they become wet; whenever mass flow rates are relatively high; when mixing slurries that are sensitive to air entrainment; or whenever discharge piping is long, has significant vertical lift, or both.
Why are Lobestar® Shear-Mixers without Radial Premixers sensitive to discharge pressure?
While entraining solid additives, the Lobestar® Shear-Mixer suction is open to atmosphere and will certainly draw free air into the slurry stream. This air forms bubbles in the slurry which gradually expand as the pressure gradient in the pipe approaches atmospheric pressure. The resulting larger bubbles within the discharge piping take up space and limit the suction flow rate. The washdown effect of the Radial Premixer provides a water seal that minimizes the volume of free air that can be drawn into the slurry.
How sensitive is the Lobestar® Shear-Mixer to discharge line pressure?
High discharge line pressure has a negative effect on the Lobestar® Shear-Mixer as well as any venturi eductor. The discharge pressure must be less than half of the motive inlet pressure of the Lobestar® Shear-Mixer for it to function. Strong consideration should be given to the discharge piping geometry, and the overall vertical lift height, as well as the number of elbows and fittings should be kept to a minimum. Increasing the discharge pipe size to a diameter larger than the Lobestar® Shear-Mixer can also help minimize the overall pressure drop through the system.
Can a slurry be recirculated to increase the solids/liquid concentration?
Yes. Lobestar® Shear-Mixers are often used in batch mixing scenarios and the molded polyurethane construction material of the nozzle and diffuser tube inserts for most standard Shear-Mixer models is preferred because of its strong resistance to abrasion. Of course, polyurethane is not chemically compatible with all types of slurries, but different materials of construction can be substituted depending on the application and slurry content.
Why is it necessary to have a valve between the additive feed line or hopper and the Lobestar® Shear-Mixer suction port?
Having a valve at the Lobestar® Shear-Mixer suction port is used during startup and shutdown of the slurry mixing pump. It should be closed during both conditions because the discharge line pressure at these times is higher than when the pump is running, and the closed valve prevents the contents of the discharge line from backing up into the feed line or hopper. At pump startup, once the required, constant motive fluid velocity for operation is established, the valve can be opened for additive introduction. The valve should always be closed prior to pump shutdown, especially if the discharge line elevation is higher than the Lobestar® Shear-Mixer, because it prevents backflow of the discharge line from the suction port.
What is the acceptable fluid velocity in the discharge piping for optimal Lobestar® Shear-Mixer function?
There is not an exact velocity for optimal function. The fluid velocity in the discharge line should be low enough to minimize overall pressure in the line, yet high enough to keep undissolved solids moving to prevent settling. In most applications, fluid velocity of 6-8 ft/sec is sufficient.
Reach Out
Contact a Vortex Ventures expert to place orders and find your next mixing solution.